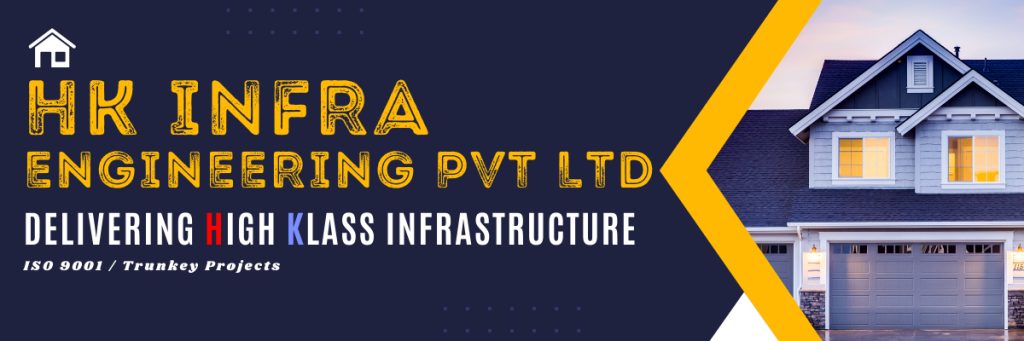
HK INFRA ENGINEERING PVT LTD.
CIVIL ENGINEERING
Our Civil interior works involve the design, construction, and renovation of interior spaces within buildings. This encompasses various aspects aimed at creating functional, aesthetic, and comfortable environments:
Space Planning
Arranging layouts to optimize the use of space, considering factors like flow, accessibility, and functionality
Interior Finishes
Selecting and applying materials for walls, floors, ceilings, and other surfaces. This can include painting, tiling, flooring, and ceiling finishes
Partitioning
Installing or modifying partitions to create separate rooms or areas within a building, often using materials like drywall, glass, or modular panels.
Lighting Design
Designing and installing lighting systems that enhance the aesthetics and functionality of a space. This includes task lighting, ambient lighting, and accent lighting.
HVAC Integration
Installing or updating heating, ventilation, and air conditioning systems to ensure comfort and air quality within the interior space.
Acoustic Treatment
Implementing solutions to manage sound and improve acoustic quality, such as soundproofing materials and acoustic panels.
Furniture and Fixtures
Selecting and installing furniture, fixtures, and equipment (FF&E) that align with the design theme and functional requirements.
Interior Signage
Designing and placing signage to guide and inform occupants within the space.
Compliance and Safety
Ensuring that all interior works meet building codes, safety regulations, and accessibility standards.
HK INFRA ENGINEERING PVT LTD.
Structural Repairing
involves diagnosing, assessing, and addressing issues in existing structures to restore their safety, stability, and functionality. This can include repairing damage caused by aging, environmental factors, accidents, or design deficiencies. Here’s a detailed overview of the structural repairing process:
Inspection and Assessment
Visual Inspection
• Initial Review: Conduct a visual inspection to identify visible signs of damage or deterioration, such as cracks, deformation, or corrosion.
• Site Conditions: Assess the condition of the site and any immediate hazards.
• Site Conditions: Assess the condition of the site and any immediate hazards.
Diagnostic Testing
• Non-Destructive Testing (NDT): Use techniques such as ultrasonic testing, radiography, or infrared thermography to detect subsurface issues without damaging the structure.
• Material Testing: Test materials (e.g., concrete strength, steel corrosion) to evaluate their current condition and suitability for repair.
Structural Analysis:
• Load Analysis: Reassess the loads and stresses on the structure to determine how the damage affects its performance.
• Failure Mode Identification: Identify the modes of failure or deterioration and their causes.
Repair Methods
Concrete Repairs
• Crack Injection: Use epoxy or polyurethane resins to fill and seal cracks in concrete.
• Surface Repair: Apply repair mortars or coatings to damaged or deteriorated concrete surfaces.
• Reinforcement: Add additional steel reinforcement or use fiber-reinforced polymers (FRPs) to strengthen weakened concrete elements.
Steel Repairs
• Rust Removal: Remove rust and corrosion from steel elements using sandblasting or wire brushing.
• Patch Plates: Install steel patch plates or additional sections to repair damaged or corroded steel members.
• Welding: Use welding techniques to repair cracks or connections in steel components.
Timber Repairs
• Reinforcement: Strengthen timber members using steel plates, additional timber, or composite materials.
• Decay Treatment: Treat and replace decayed or damaged wood using preservative treatments and new timber sections.
• Structural Reinforcement: Install additional supports or braces to address structural deficiencies.
Masonry Repairs
• Repointing: Replace damaged mortar in masonry joints to restore strength and stability.
• Brick Replacement: Replace cracked or damaged bricks with new ones, ensuring proper bonding and alignment.
• Reinforcement: Add reinforcement, such as steel ties or mesh, to improve the structural integrity of masonry walls.
Repair Design
• Repair Plan: Develop a detailed repair plan that includes methods, materials, and procedures for addressing identified issues.
• Design Considerations: Ensure that repairs are designed to restore or improve structural capacity and durability.
• Compliance: Verify that repair methods comply with relevant building codes and standards.
Implementation
• Repair Execution: Carry out repairs according to the approved plan, ensuring that all work is performed safely and accurately.
• Quality Control: Monitor the quality of repair work to ensure it meets design specifications and performance criteria.
• Documentation: Keep detailed records of all repair activities, including materials used, methods applied, and any changes to the original plan.
Post-Repair Evaluation
• Inspection: Conduct a final inspection to verify that all repairs have been completed to the required standards.
• Testing: Perform any necessary tests to confirm that the repaired structure meets safety and performance requirements.
• Monitoring: Implement a monitoring plan to track the performance of the repaired structure over time and detect any future issues.
Preventive Measures
• Maintenance Plan: Develop a maintenance plan to regularly inspect and maintain the structure to prevent future damage.
• Protective Coatings: Apply protective coatings or treatments to enhance the durability of repaired elements and prevent further deterioration.
Safety and Compliance
• Safety Measures: Ensure that all repair work adheres to safety regulations and practices to protect workers and the public.
• Regulatory Compliance: Ensure that repairs comply with local building codes, standards, and regulations.